Over the summer while dining at Hotel Congress, Del Hendrixson Jr. noticed signs set out about straws.
“We only serve straws upon request,” read the signs, which are part of an environmental movement to reduce plastic waste.
Hendrixson runs a printing business — designing and printing artwork for businesses to infuse onto glass products, such as jewelry and beer mugs.
But when he sat at Hotel Congress, he realized he could take his business to the next level. And although he could “see the writing on the wall” months prior, Hendrixson decided to dip his toes into the glass-straw business.
The concept of glass straws isn’t a new one, but Hendrixson says his straws are different.
“I saw so many people starting to make glass straws, but they couldn’t put logos on them,” Hendrixson says.
“We can make logos. So, we just said one day, ‘Why don’t we make glass straws?’”
Each of Hendrixson’s straws, which are made in a warehouse near Armory Park, feature detailed designs.
Some say things like “Tucson cares.” Others sport business logos.
And while it doesn’t take a whole lot of time to make the straws in bulk, the individual process can be a tedious one.
It takes Hendrixson’s team about two hours to complete each straw, which includes cutting long glass tubes, flame-polishing the ends, then printing the designs using pigment and water slide paper.
With the help of a little water, the designs are infused onto the straws, which then go into a kiln at 1,100 degrees. Once they’re cooled, they’re finished.
Although the process includes many detailed steps, Hendrixson says his team can make around 500 straws in that two-hour time frame.
Hendrixson says he’s happy he gets to do something that allows him to be creative — especially when it also helps the environment and those working in animal conservation.
“I’m into prevention — preventing people from committing crimes, people from hurting each other,” Hendrixson says. “So I thought this was also a perfect opportunity to prevent something. Why shouldn’t we, as people, do something to help sea animals?”
He also says that as straw orders increase, he plans to work with the community to provide outreach opportunities.
“Every single level of this straw (business) is helping someone,” he says.
Hendrixson says he’s made straws for several local businesses, including Hotel Congress, Maynards Market & Kitchen and Magpies Gourmet Pizza.
Since summer, Fourth Avenue’s Pop Cycle, which is known for its up-cycled products, has carried the straws.
Store Manager Libby Tobey says customers love them.
“With our store and our motto, we really liked the product,” she says. “We’ve enjoyed carrying them — and that it’s a local business and they’re eco-friendly.”
For more information, head to iloveglassstraws.com
Photos: Tucson business breaks into glass straw production
Glass straws
Updated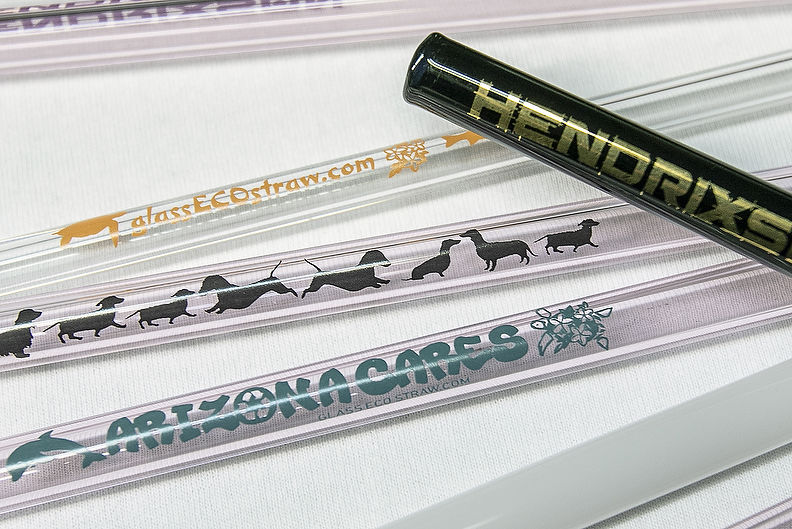
Glass straws are manufactured at Tucson-based iloveglassstraws.com. The straws, made from borosilicate glass and printed with borosilicate infused decals, are produced as alternatives to plastic straws.
Glass straws
Updated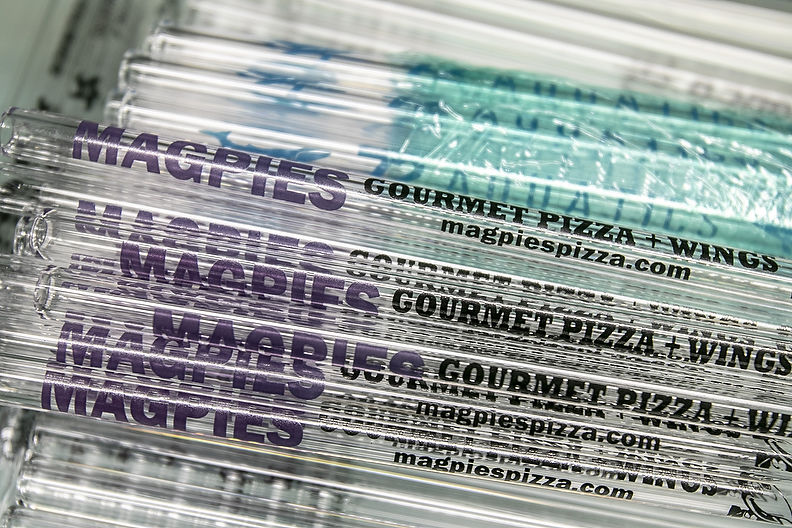
Glass straws manufactured at Tucson-based iloveglassstraws.com. The straws, made from borosilicate glass and printed with borosilicate infused decals, are produced as alternatives to plastic straws.
Glass straws
Updated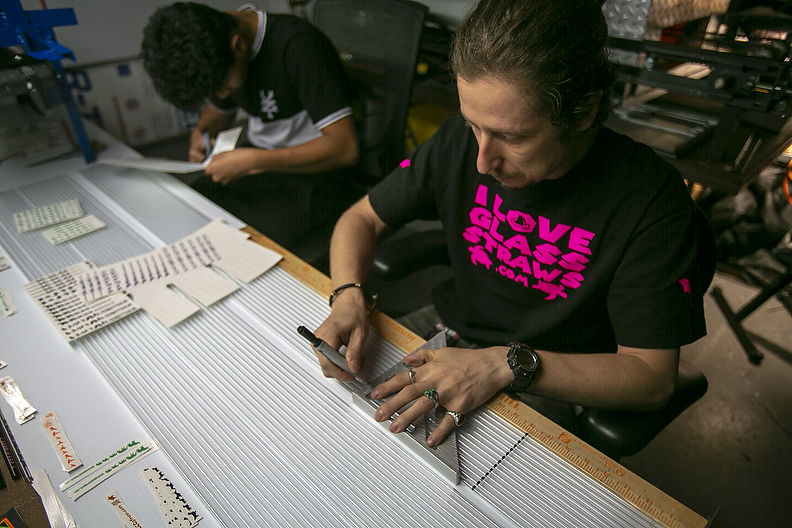
Ricky Segura, project manager at Tucson-based iloveglassstraws.com, marks borosilicate glass tubes to be scored and cut to size at a small warehouse in Tucson, AZ. on January 9, 2019. The straws, made from borosilicate glass and printed with borosilicate painted decals, are offered to companies as alternatives to plastic straws.
Glass straws
Updated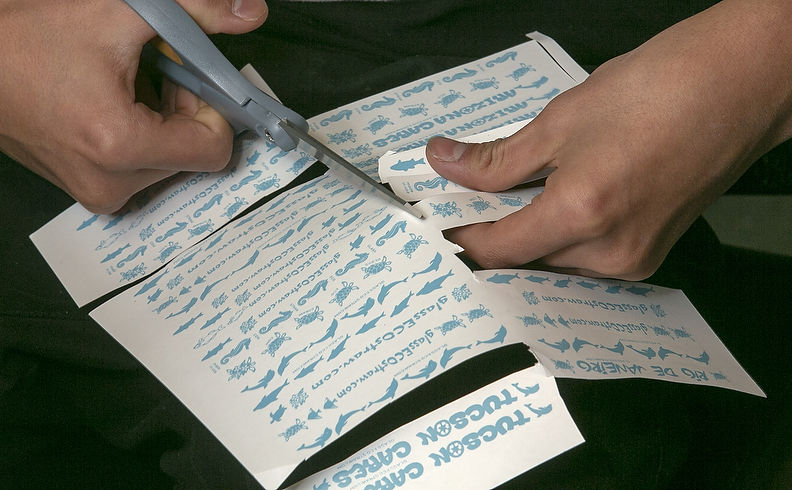
Xavier Mungia cuts decals printed with borosilicate paint at Tucson-based iloveglassstraws.com, in Tucson, AZ on January 9, 2019.
Glass straws
Updated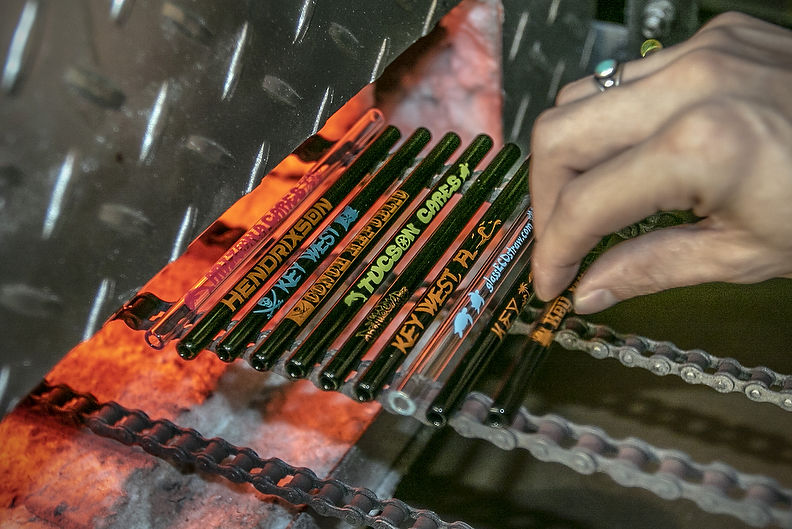
Borosilicate printed decals are hand set on each straw and then fired in a custom-made belt-driven kiln at Tucson-based iloveglassstraws.com in Tucson, AZ. The borosilicate printed decals fuse to the borosilicate straw making the printing essentially impervious to scratching or removal.
Glass straws
Updated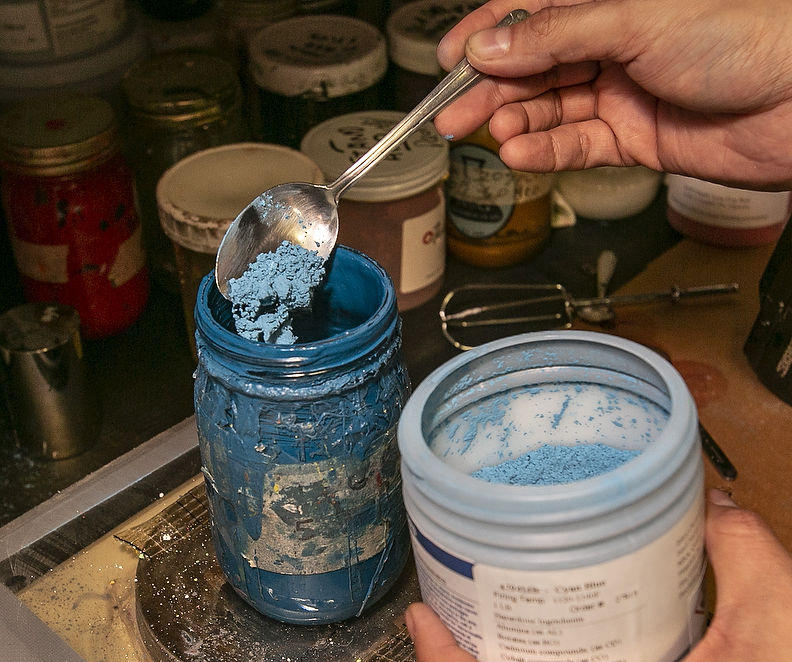
Borosilicate paint is mixed in custom colors to exacting standards at Tucson-based iloveglassstraws.com. The borosilicate printed decals fuse to the borosilicate straw making the printing essentially impervious to scratching or removal.
Glass straws
Updated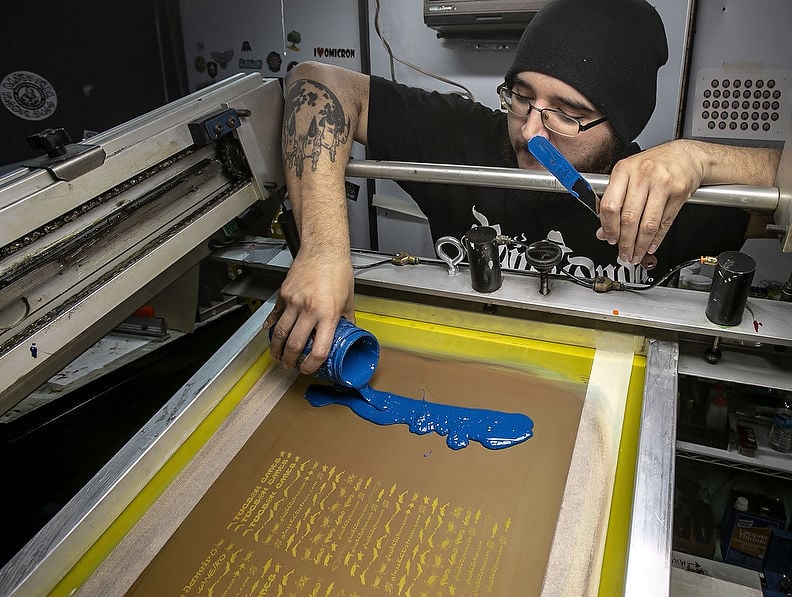
Senior pressman Cisco Valencia applies a blue borosilicate paint onto a printing plate to be printed onto waterslide decal paper at Tucson-based iloveglassstraws.com in Tucson, AZ on January 9, 2019.
Glass straws
Updated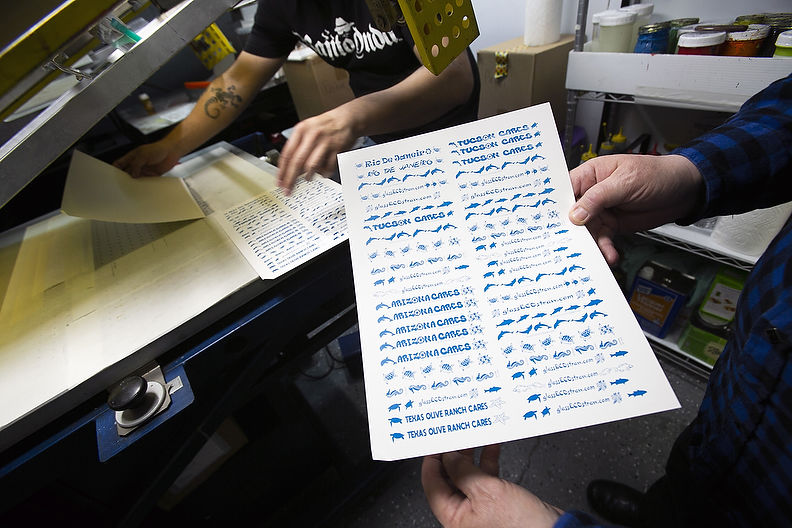
Sheets of blue waterslide decals printed with borosilicate paint come off the press individually at Tucson-based iloveglassstraws.com in Tucson, AZ on January 9, 2019.
Glass straws
Updated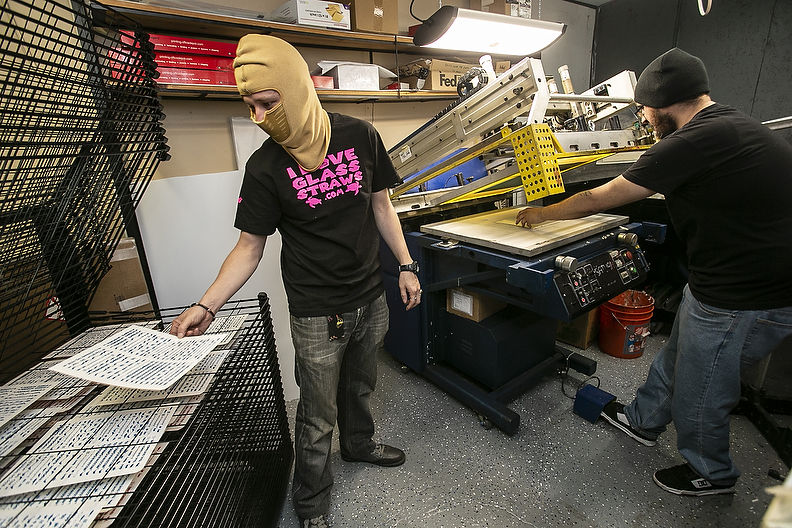
Ricky Segura, left, and Cisco Valencia, from left, make sheets of blue borosilicate waterslide decals one at a time at iloveglassstraws.com in Tucson, AZ on January 9, 2019. The sheets are air dried and cured on a drying rack.
Glass straws
Updated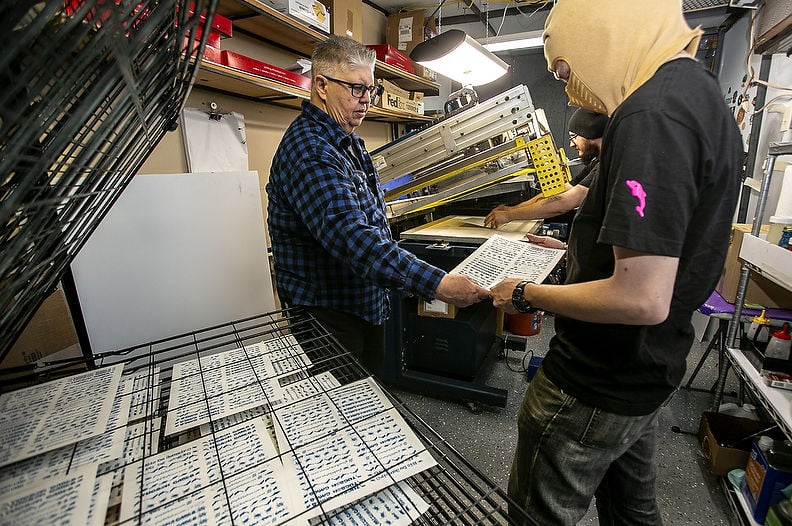
Del Hendrixson, Cisco Valencia and Ricky Segura, from left, make sheets of blue borosilicate waterslide decals one at a time at iloveglassstraws.com in Tucson, AZ on January 9, 2019.
Glass straws
Updated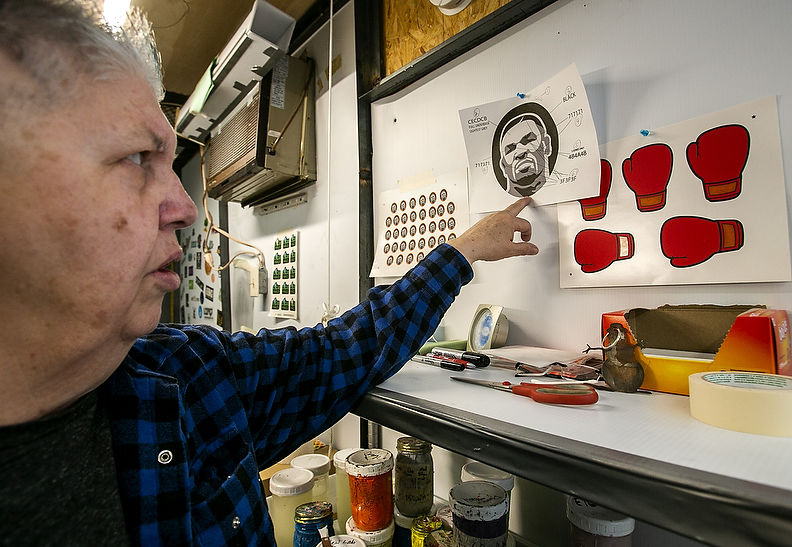
Del Hendrixson explains the printing process he used on a project for boxer Mike Tyson using 24K gold based paint at iloveglassstraws.com in Tucson, AZ.
Glass straws
Updated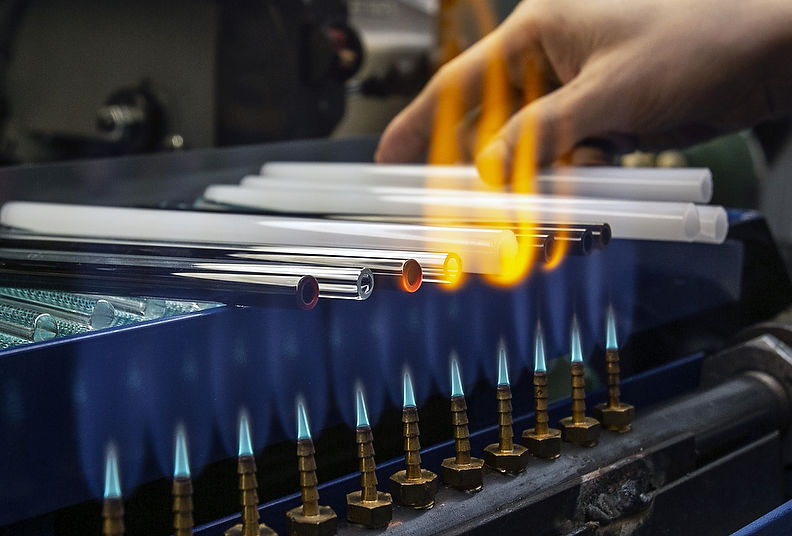
Glass straws pass over a set of flames on a polisher designed by Del Hendrixson to smooth the sharp raw ends of the scored glass straws at iloveglassstraws.com in Tucson, AZ on January 9, 2019. A properly tuned propane flame is hot enough to melt the glass to a smooth, rounded end.
Glass straws
Updated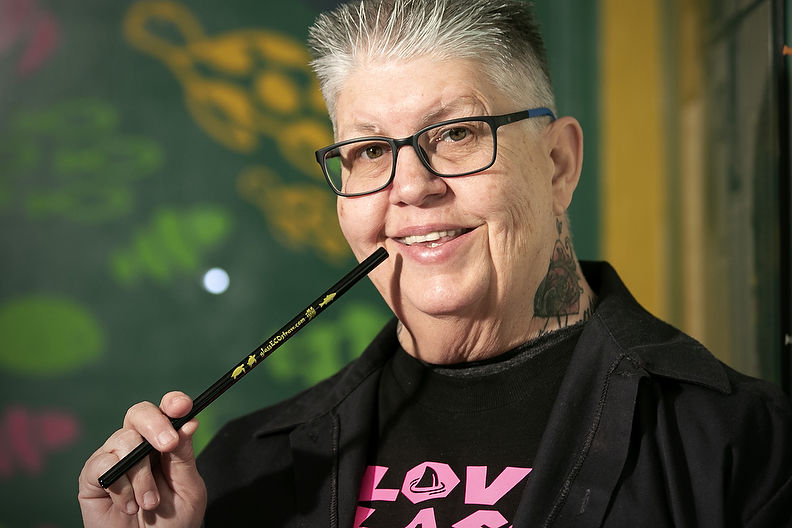
Del Hendrixson with a printed glass straw at iloveglassstraws.com in Tucson, AZ on January 9, 2019. Prior to founding iloveglassstraws.com, Hendrixson used his printing business to print designs for glass products, such as beer mugs and jewelry.