When Carly Quinn strolls into her shop and studio, past colorful tiles stacked on tables and hung on walls, she is in her element.
The design studio at 730 S. Stone Ave. is hers — well, almost hers. She's renting to own with a year to go.
She and her small staff have been crafting decorative tiles in the 1800-square-foot space since May. Quinn, 33, turned her art into her full-time job about seven years ago.
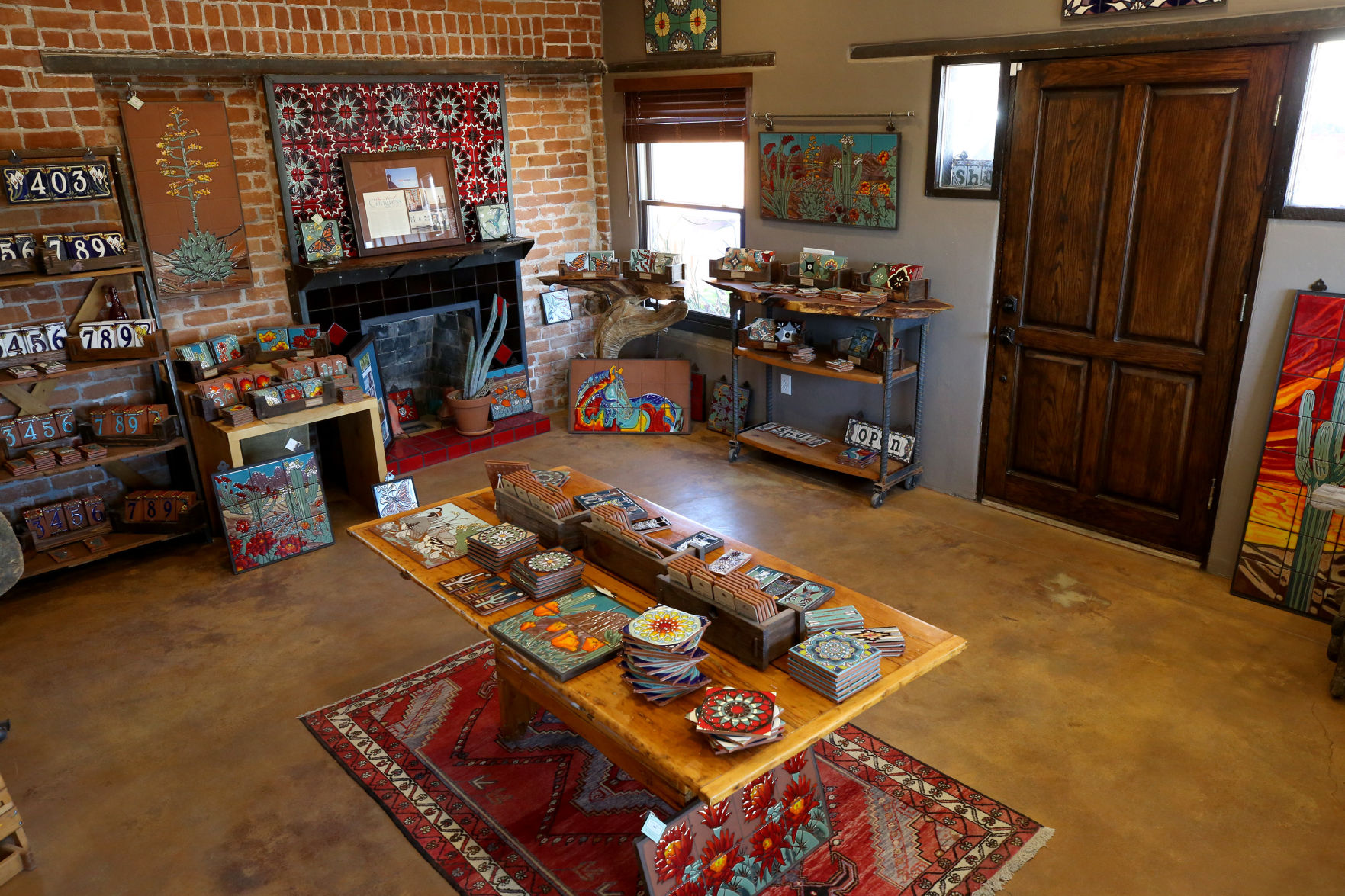
Colorful examples of tile art in the showroom of Carly Quinn Designs at her shop near downtown Tucson on Feb. 8, 2018. Quinn left a full time job to devote herself to creating the design on her tiles.
Now she runs Carly Quinn Designs and employs three women full time and another part time. She does custom tiles for clients around the world, with her art in gift shops at four international airports. She designs pieces for wholesale and residential clients.
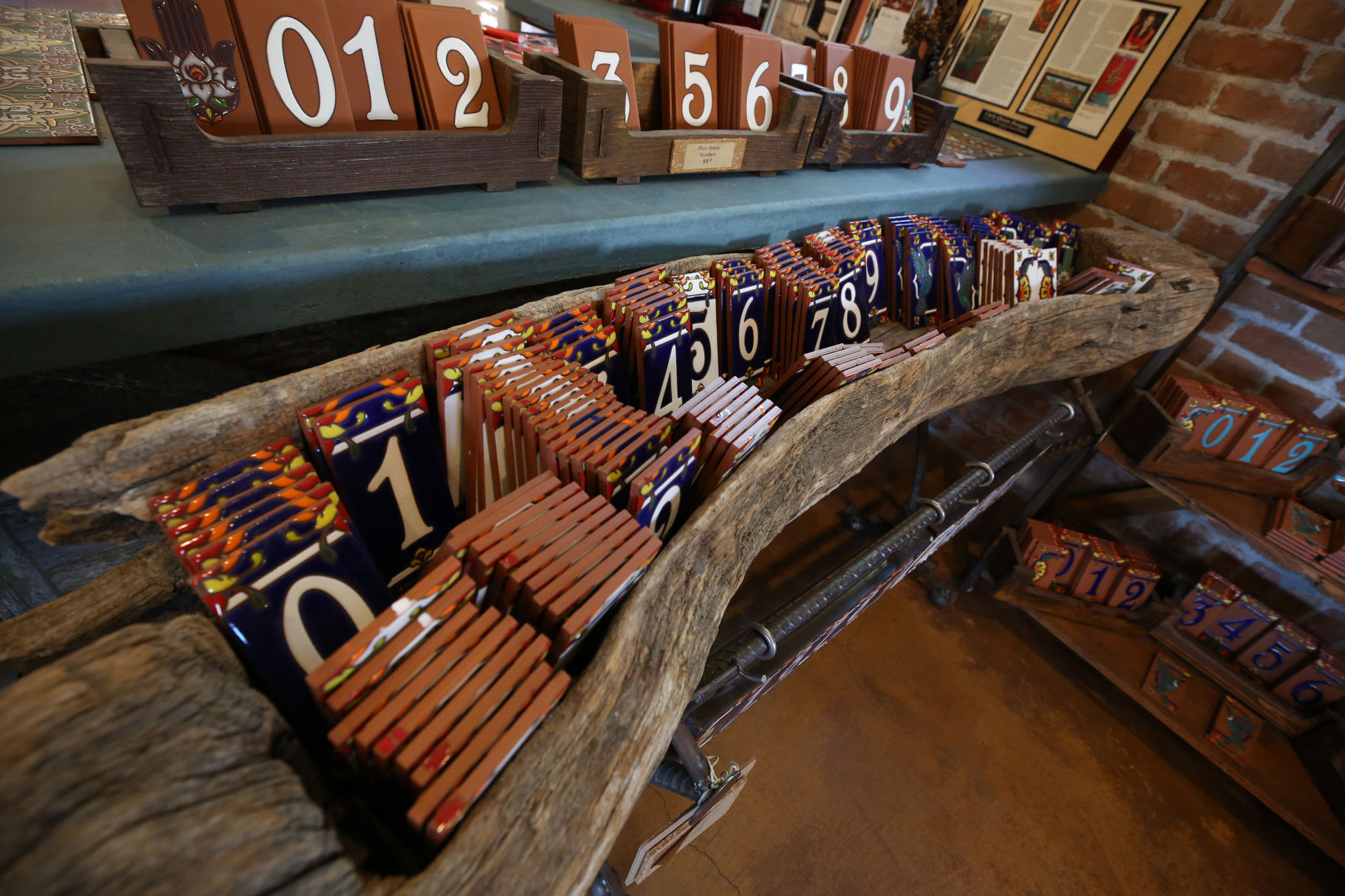
House numbers are stacked inside the mesquite tree trough at Carly Quinn Designs.
Her tiles are gorgeous and vibrant, bearing artful designs and desert scenes. Many have pops of a rich red, Quinn's favorite color.
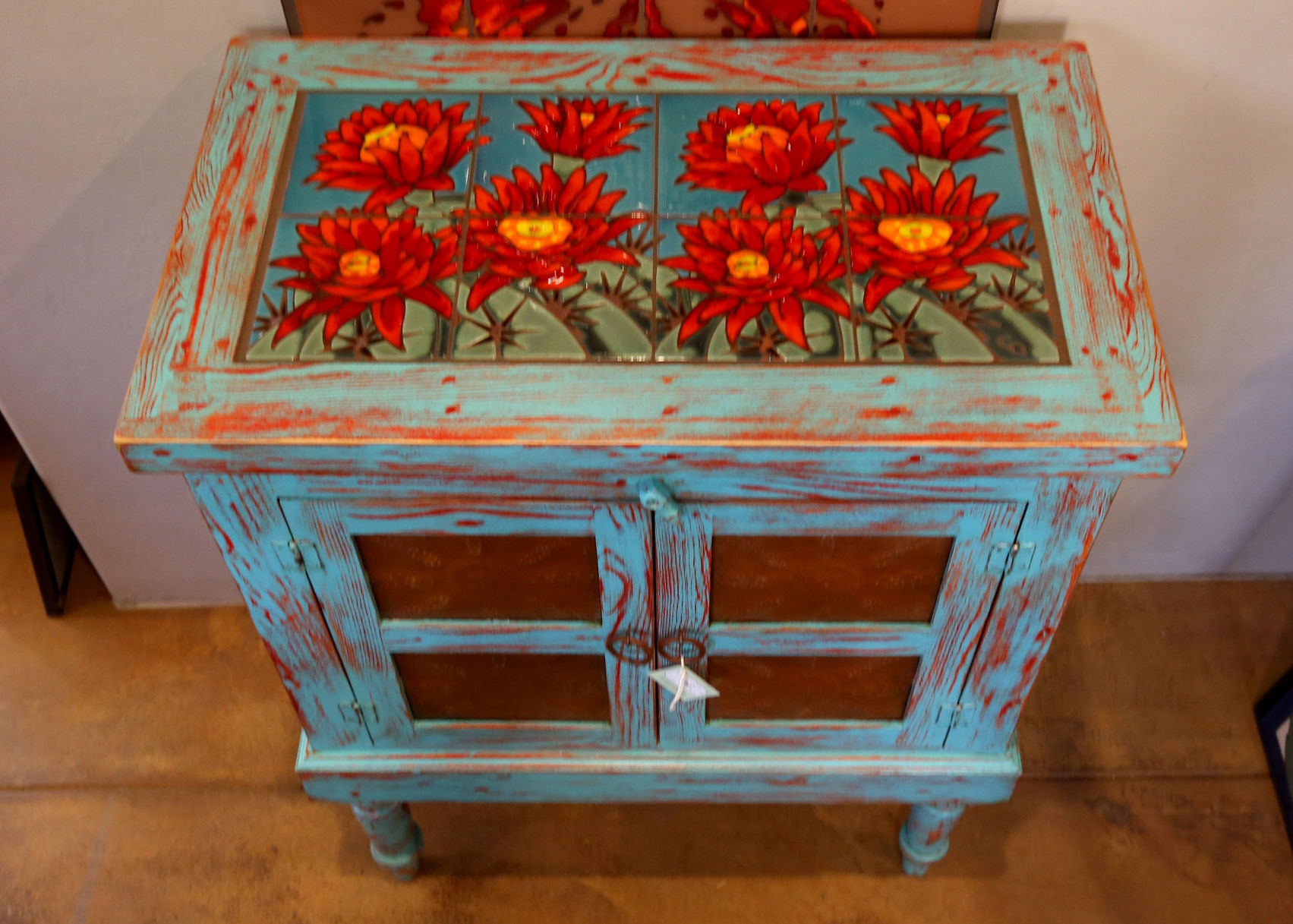
Colorful tiles sit atop a piece of furniture at Quinn's shop.
Originally from Prescott, Quinn came to Tucson to attend the small private Art Center Design College (now Southwest University of Visual Arts). She had always planned to make art. Her grandmothers passed on their artistry to their granddaughter, and Quinn briefly considered selling her paintings.
But it's tile that stole her heart.
After moving to Tucson, she got a job working for a tile artist. She spent about two years there where she learned a Moorish technique called Cuerda Seca that she uses in her own work today.
"As soon as I graduated college, I knew I gotta find out a way to make tile and make a living out of it," she says. "It's what I love to do."
Quinn graduated with a degree in illustration and fine art and a minor in graphic design. For several years she worked a full-time job as a graphic designer, hating the desk job, wanting to make art.
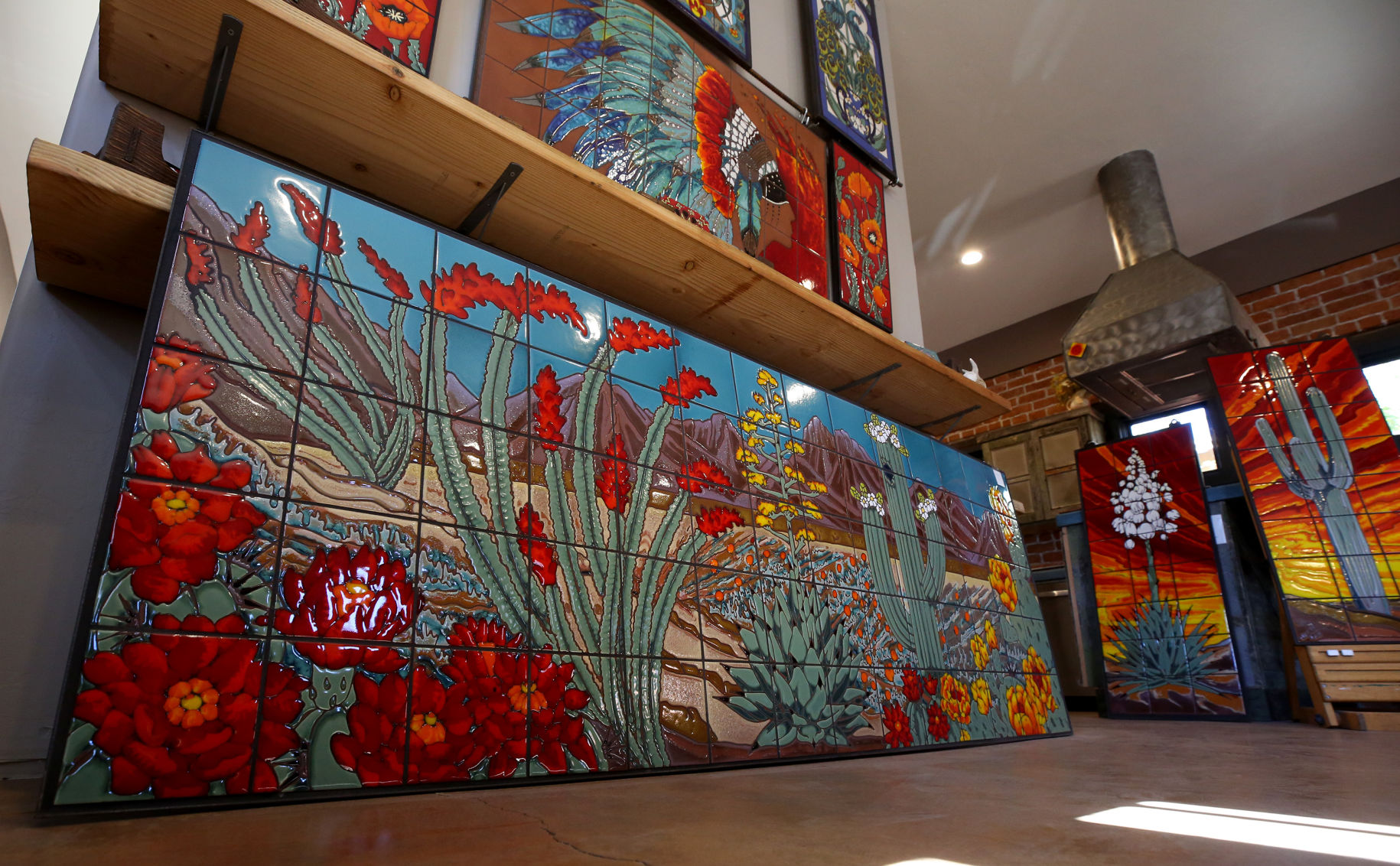
Quinn's clients often want desert scenes when they commission pieces from her.
She saved up enough to buy a small kiln and rent a 200-square-foot space behind the Walmart on Grant Road and Alvernon Way.
"I just couldn't sit at a desk any more, and I had such a drive to be my own boss and make artwork for myself," she says. Her boyfriend — now her husband — is the one who encouraged her to just do it, to just leave that job.
Quinn says she worked her last job two years longer than she wanted to.
"I was so scared of leaving that stability and thought who is going to want to buy my stuff?"
When she left that job in early 2011, she says she had $800 and a kiln. Slowly she began to grow, hopping into larger studios, eventually settling in the Warehouse Arts District near Tap & Bottle.
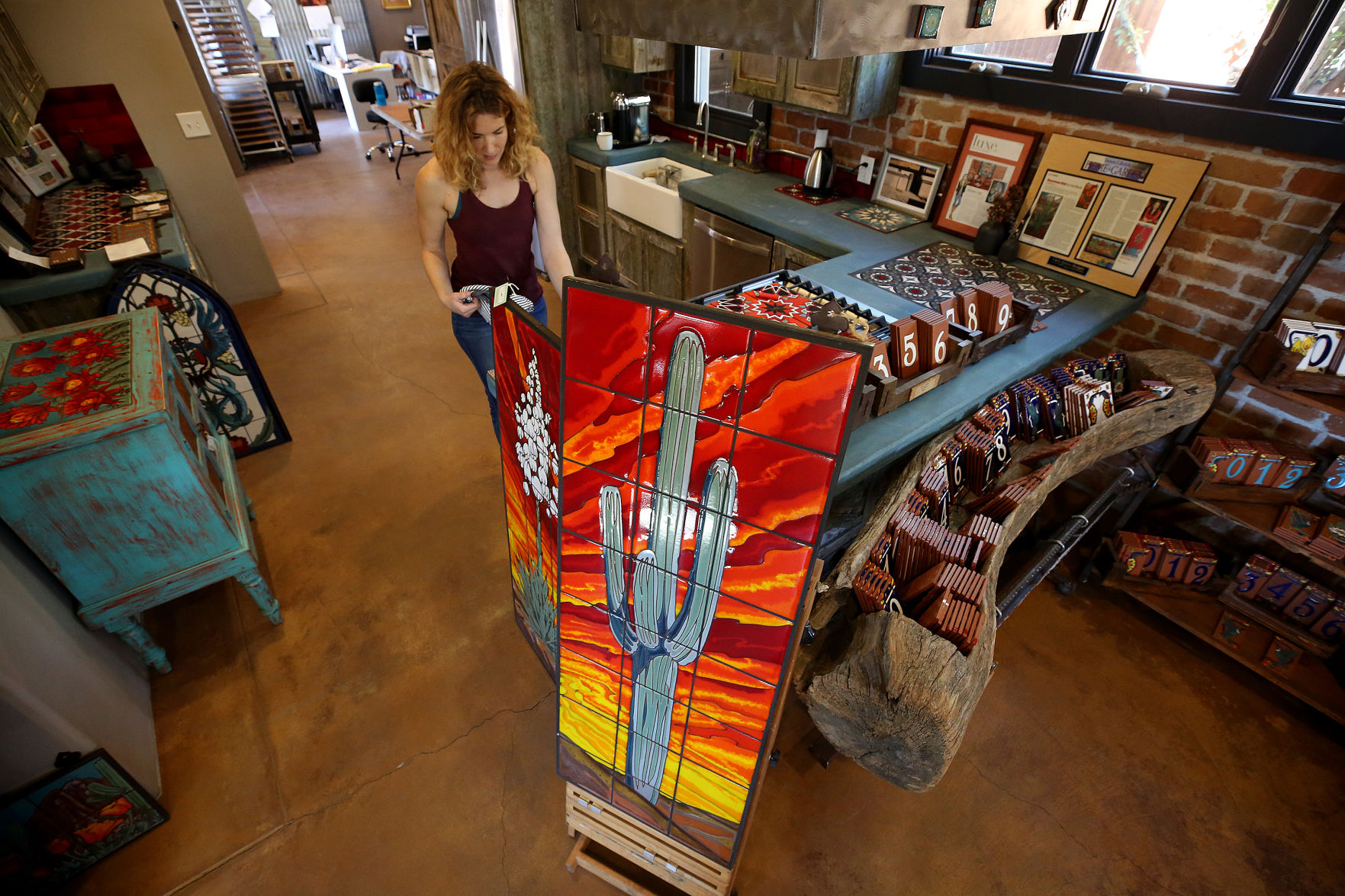
Quinn had several shops in the Warehouse Arts District before ending up in her showroom and studio just south of downtown.
"It's been a steady upward trajectory since I started," she says, adding that as a small business it's still "absolutely terrifying sometimes. ... Money comes in and it goes right out. I have to make sure bills are paid and payroll is met ... and my paycheck is the first one to go if it ever needs to."
An early gig with the Sky Island Alliance to make small awards bearing local plants gave her a comfort level with desert flora — a must-have when so many clients want desert scenes in the tile work they commission. Already a hiker and lover of the outdoors, that hasn't been hard for Quinn.
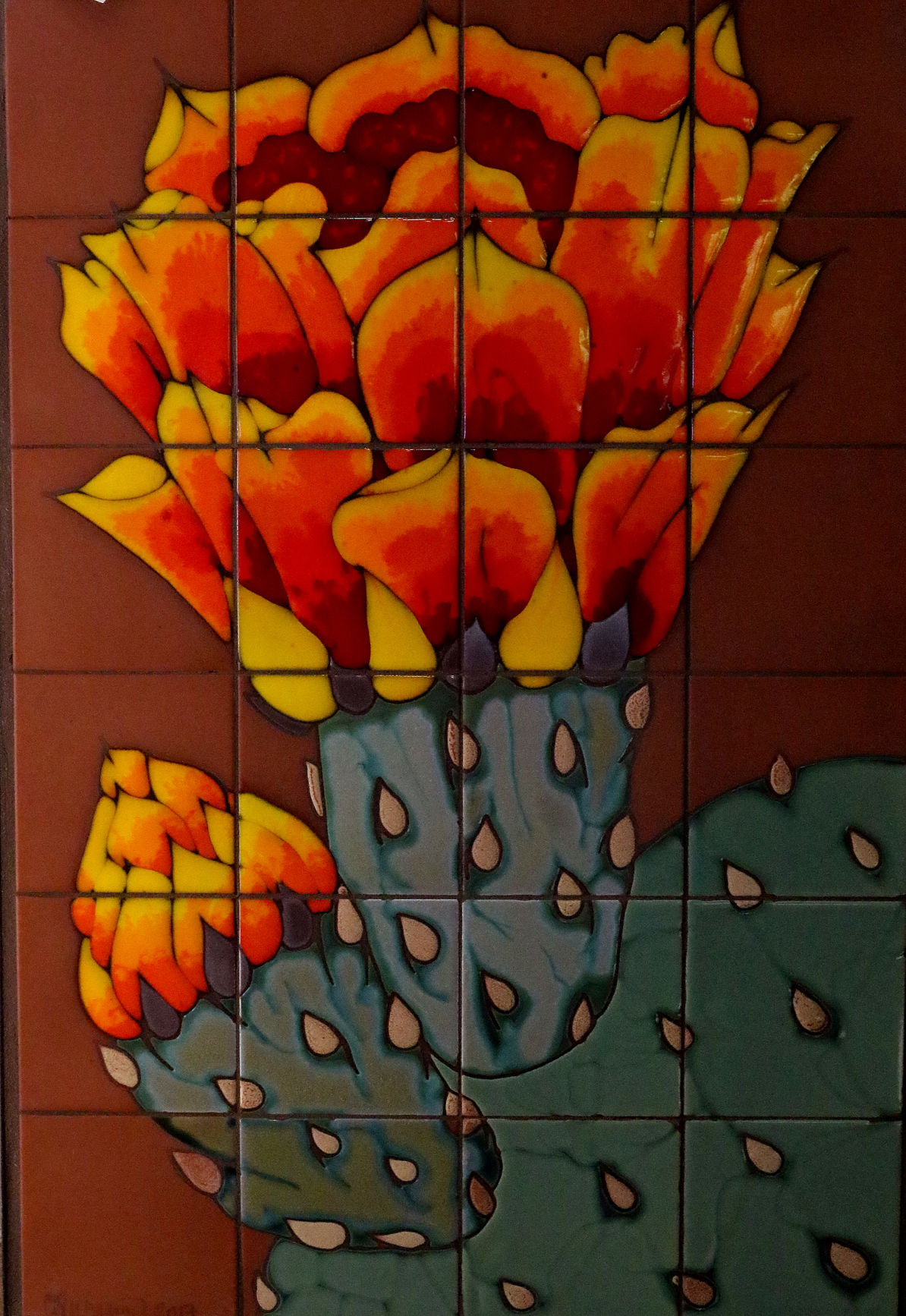
A cactus bloom tile is in the showroom at Carly Quinn Designs near downtown.
Arabesque styles "that are Moorish in origin, probably from the 1500s" from areas such as Turkey and Morocco influenced her work early on, though she has since transitioned to a more Southwestern flair to cater to local clients.
Most days, Quinn opens the shop and studio at 11 a.m., when her day often begins with sketching designs for custom projects. Much of the rest of her day falls to painting or moving tiles in and out of one of the four kilns at her studio.
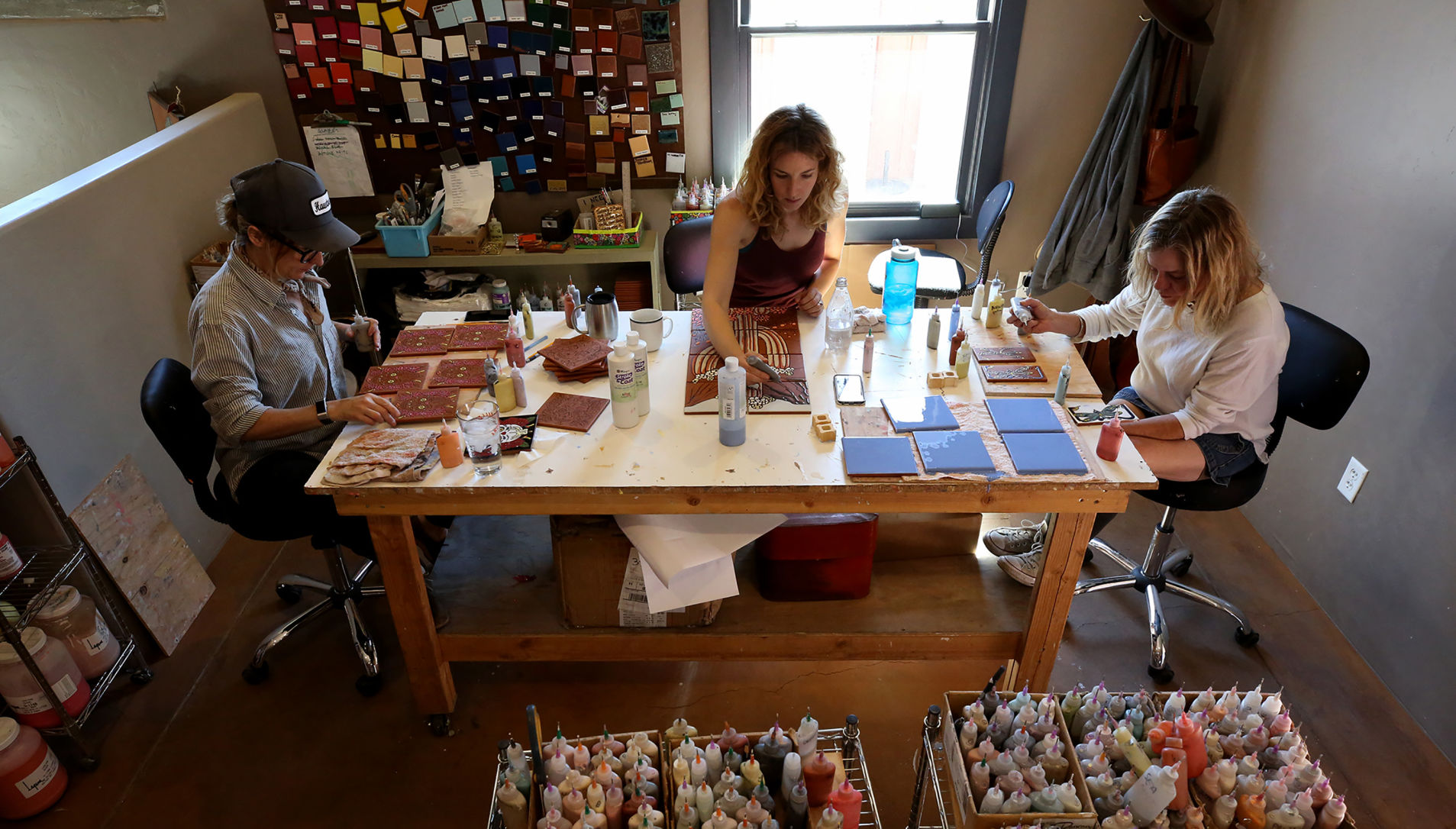
Carly Quinn, middle, works together with Dani Hawley, left, and Sarah Smith.
Here's how she does it, how she transforms plain ceramic tiles into bright works of art.
1. The first step is drawing the design for the piece.
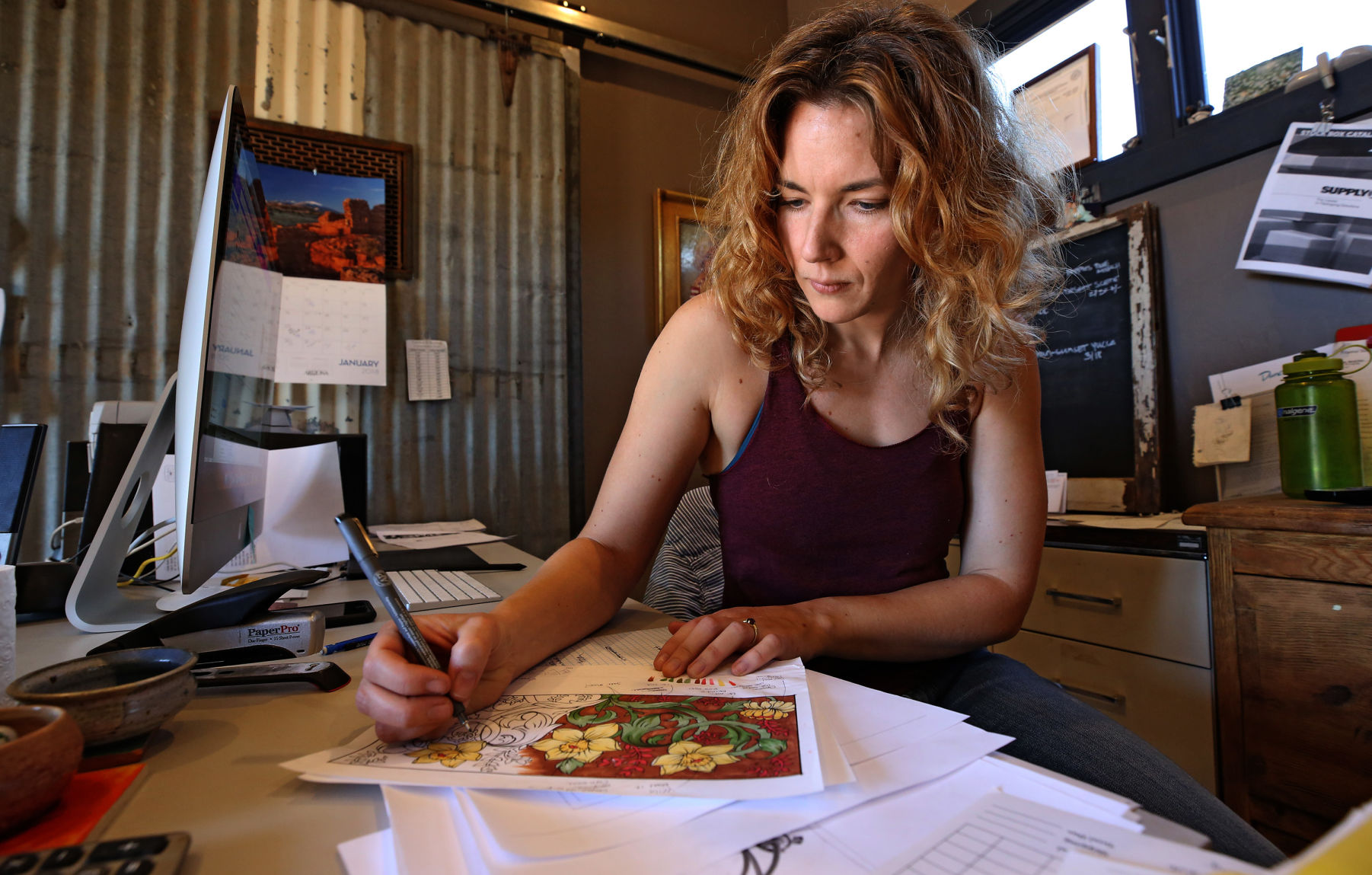
Carly Quinn sketches out a design.
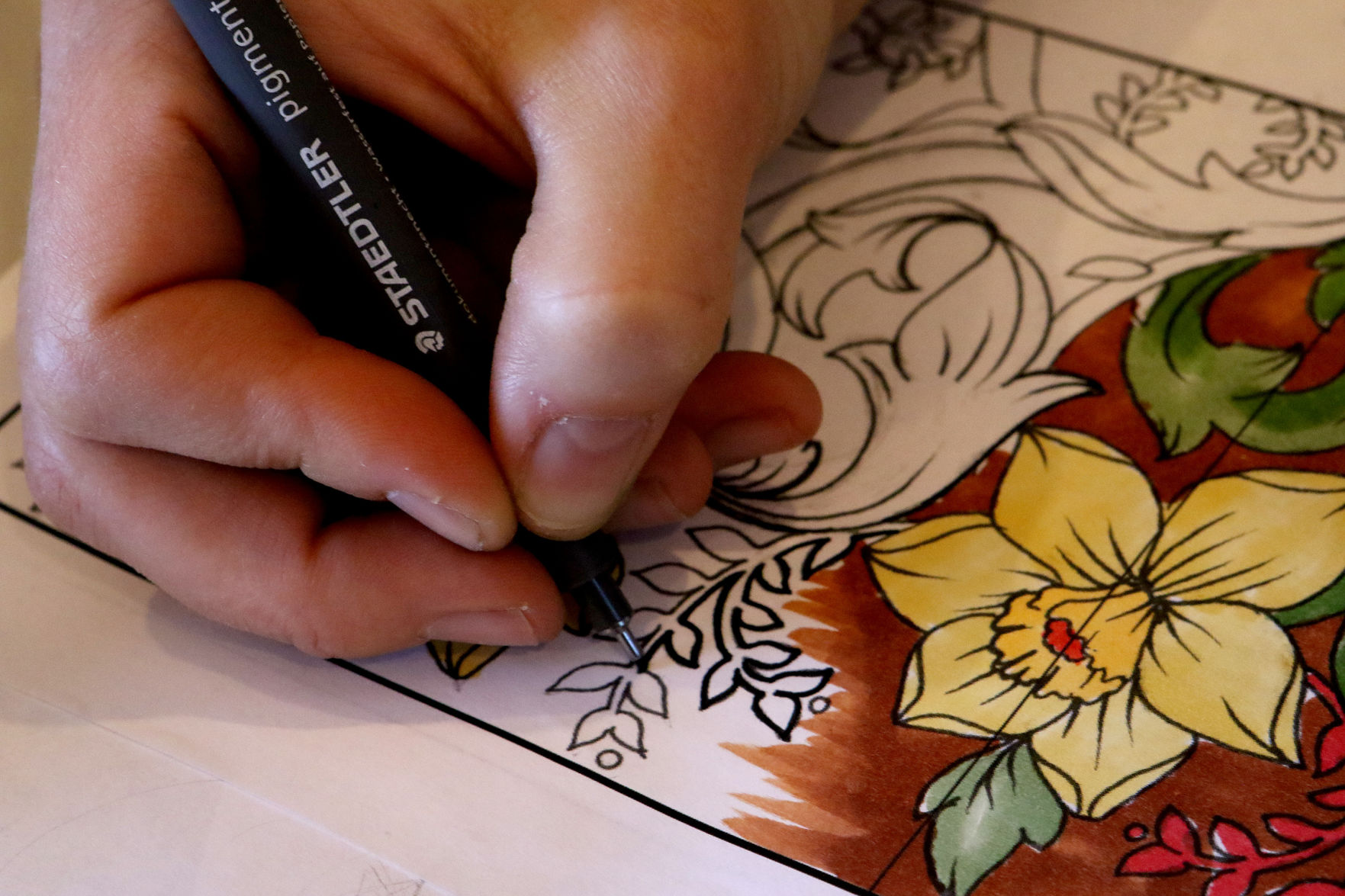
Quinn creates custom designs for many of her clients.
2. The drawing is then transferred onto the ceramic tile and outlined with wax, which once dry, keeps the glaze more or less in place while the tile is painted. Quinn has automated this process with silkscreen printing for tiles she makes in bulk.
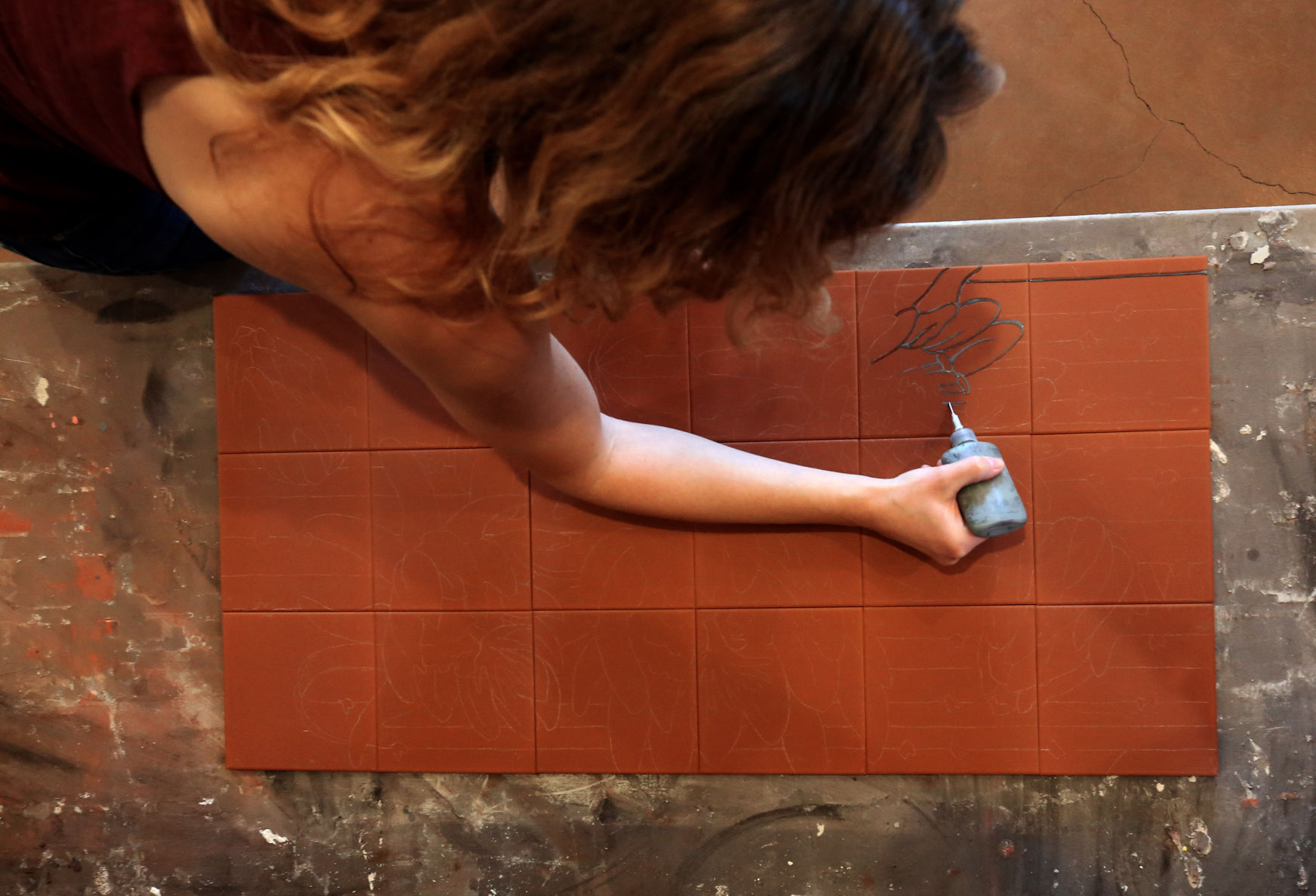
Quinn does a wax transfer.
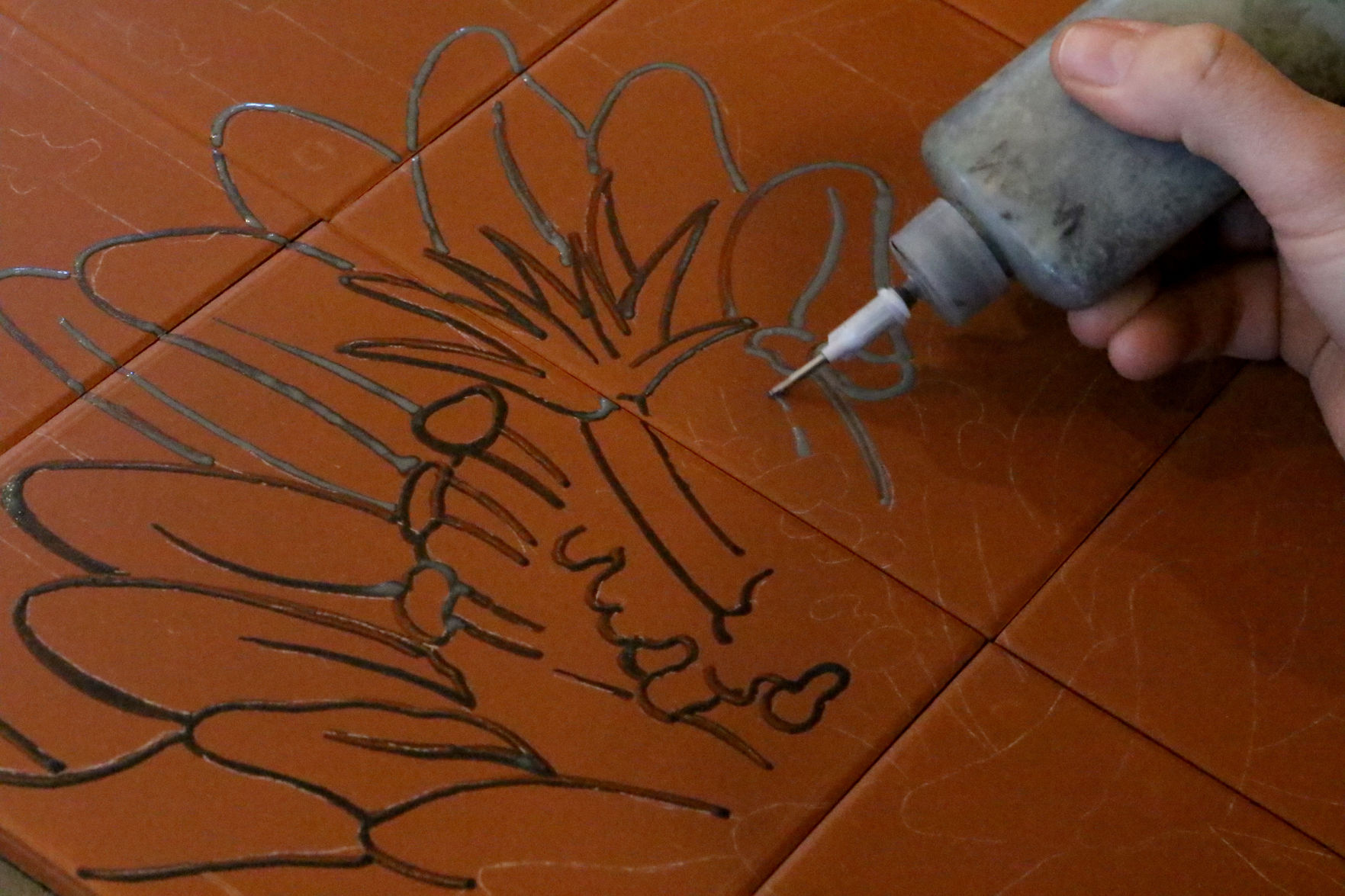
The wax transfer acts as a outline for the painting Quinn will do later.
3. Then the painting process, where colors blend beautifully. Quinn uses a ceramic glaze.
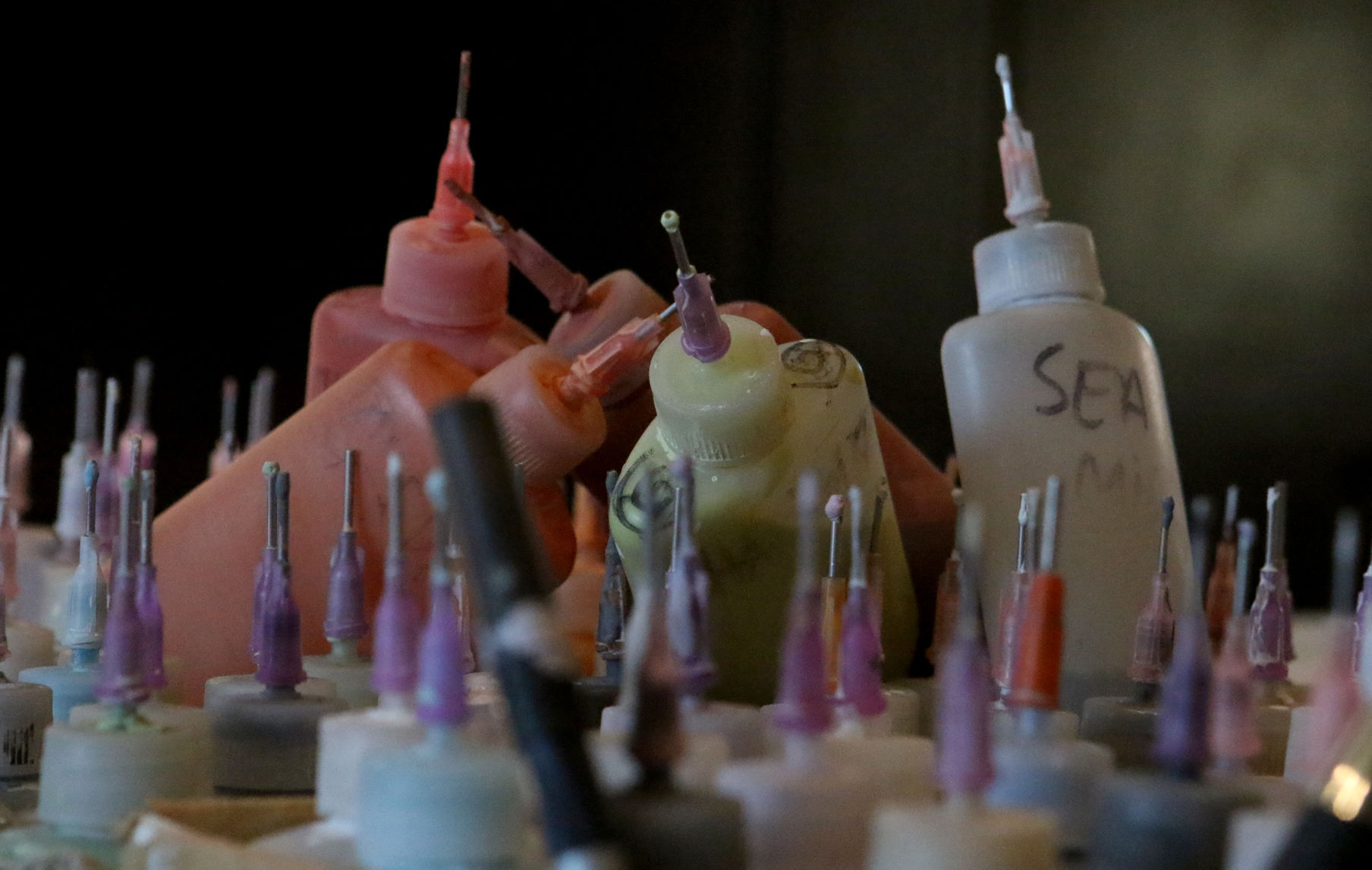
Several tubes of ceramic glaze are askew at Quinn's shop near downtown.
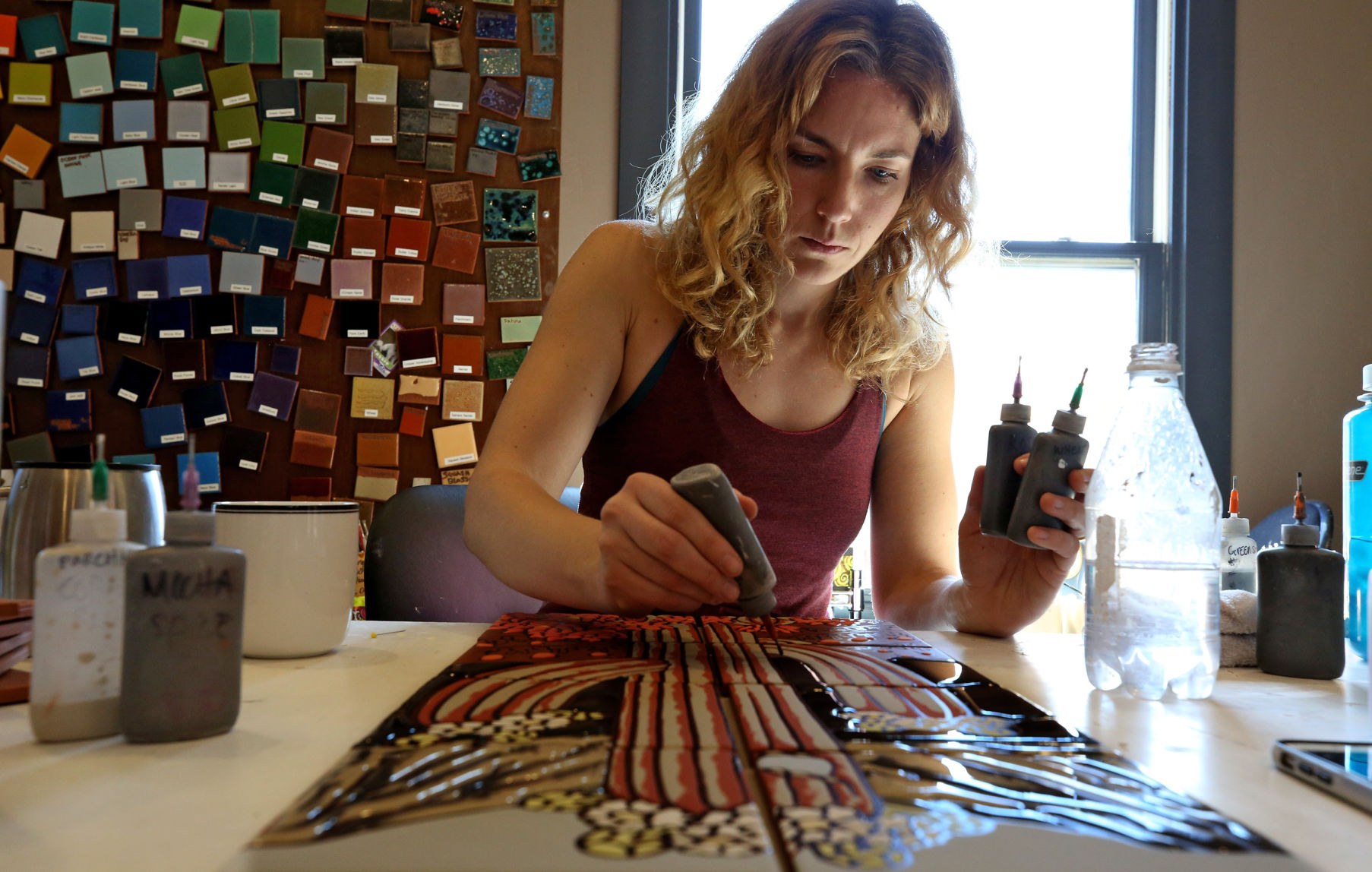
Carly Quinn applies a glaze to a piece she is working on.
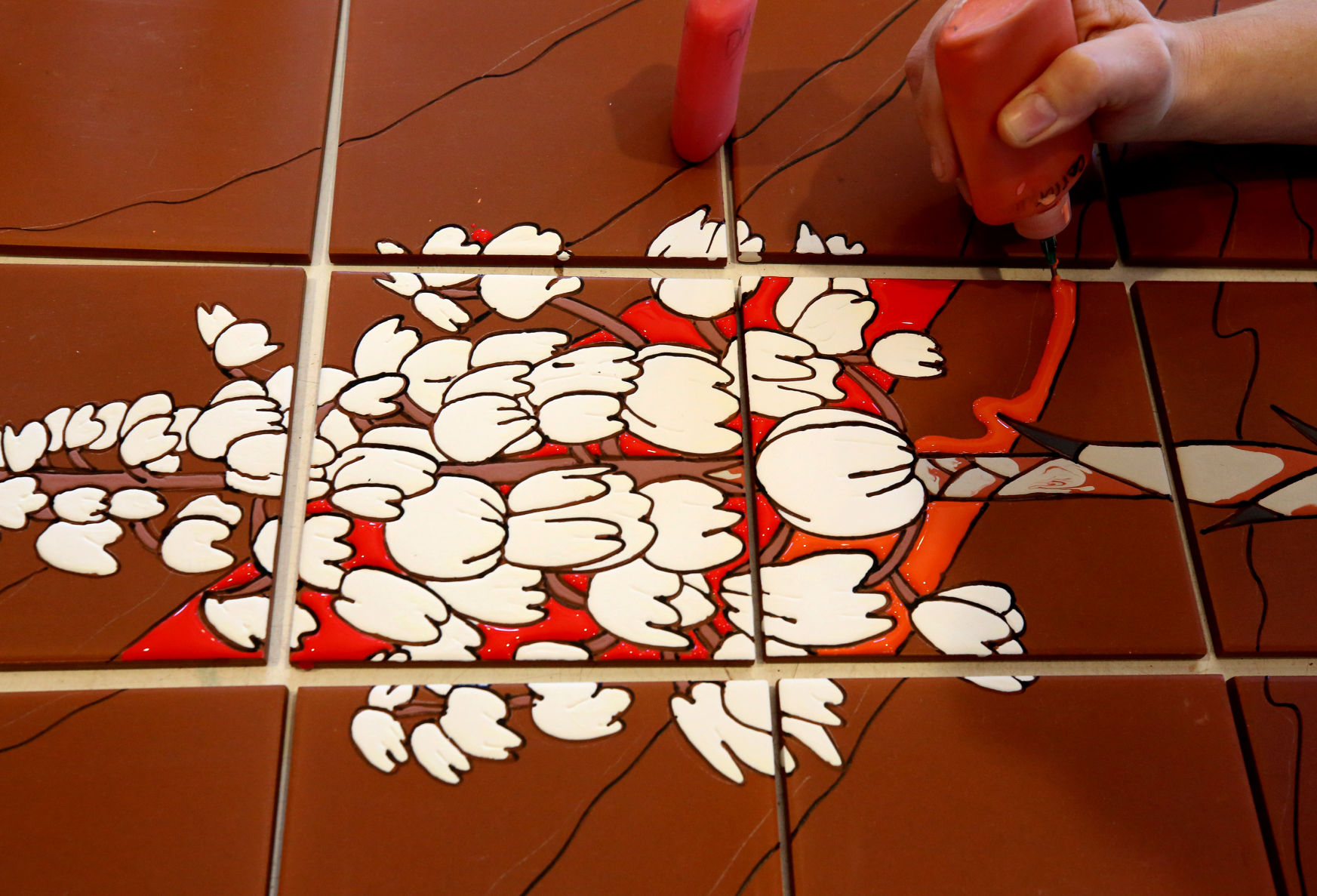
Quinn adds the glaze to a yucca she is painting.
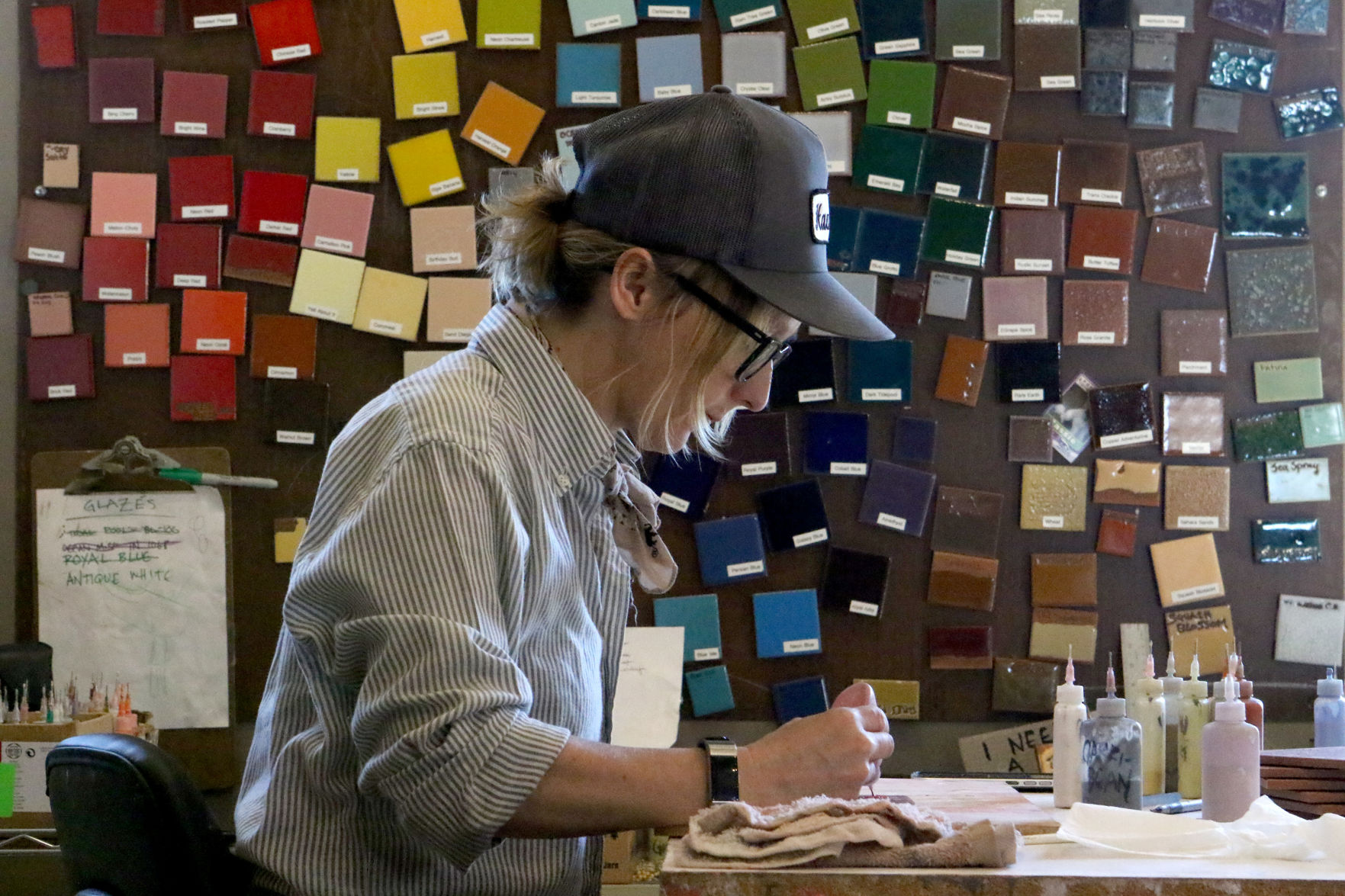
Dani Hawley paints some tile pieces at Quinn's shop.
5. Tiles are transferred to the kiln every day where they are fired between 1800 and 2000 degrees Fahrenheit for 24 hours. When the tiles finally cool, the glaze has hardened like glass. Now they're ready for installation!
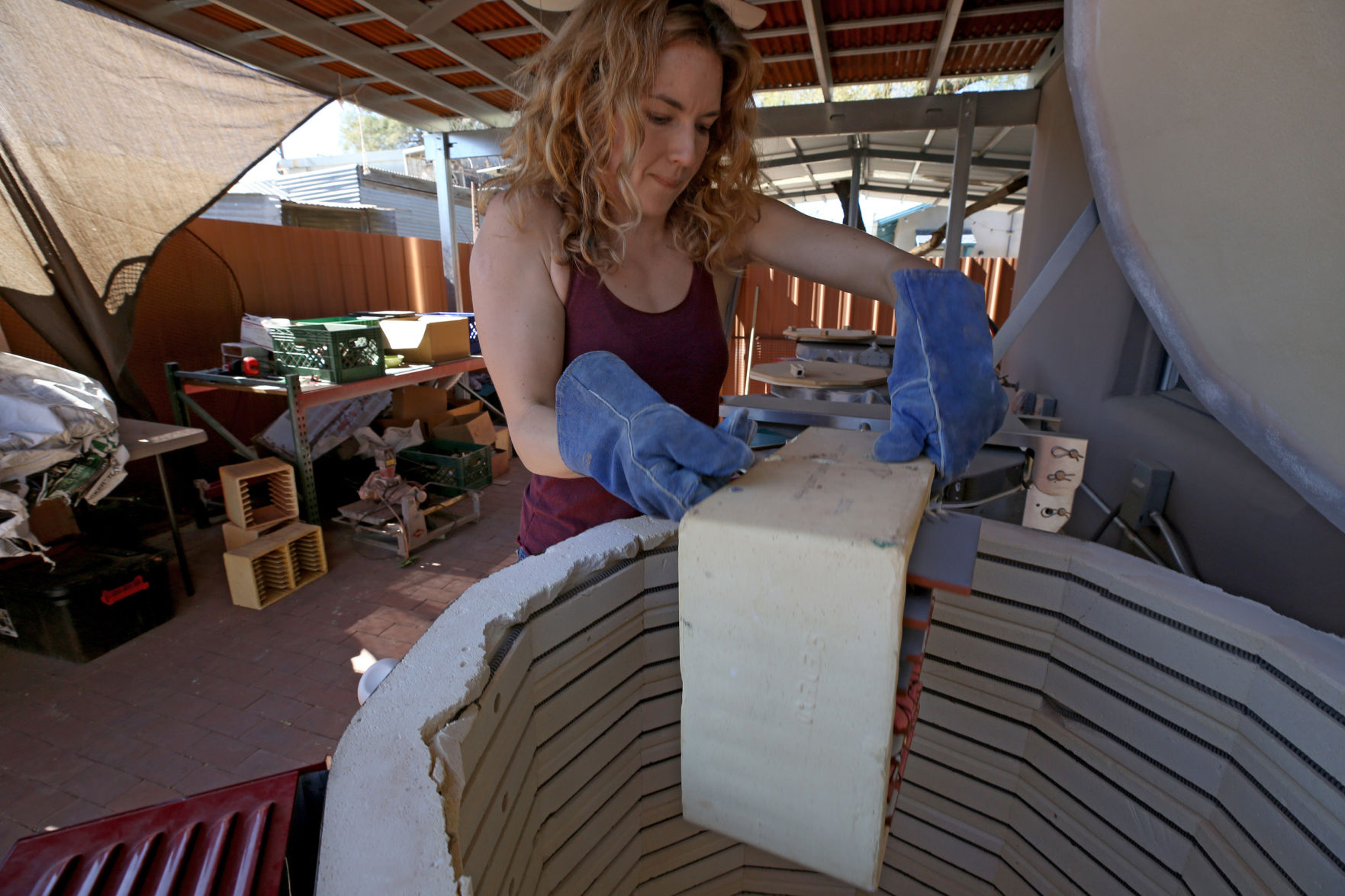
Carly Quinn loads a tile rack into a kiln as she demonstrates the technique she uses to create colorful decorative tiles.
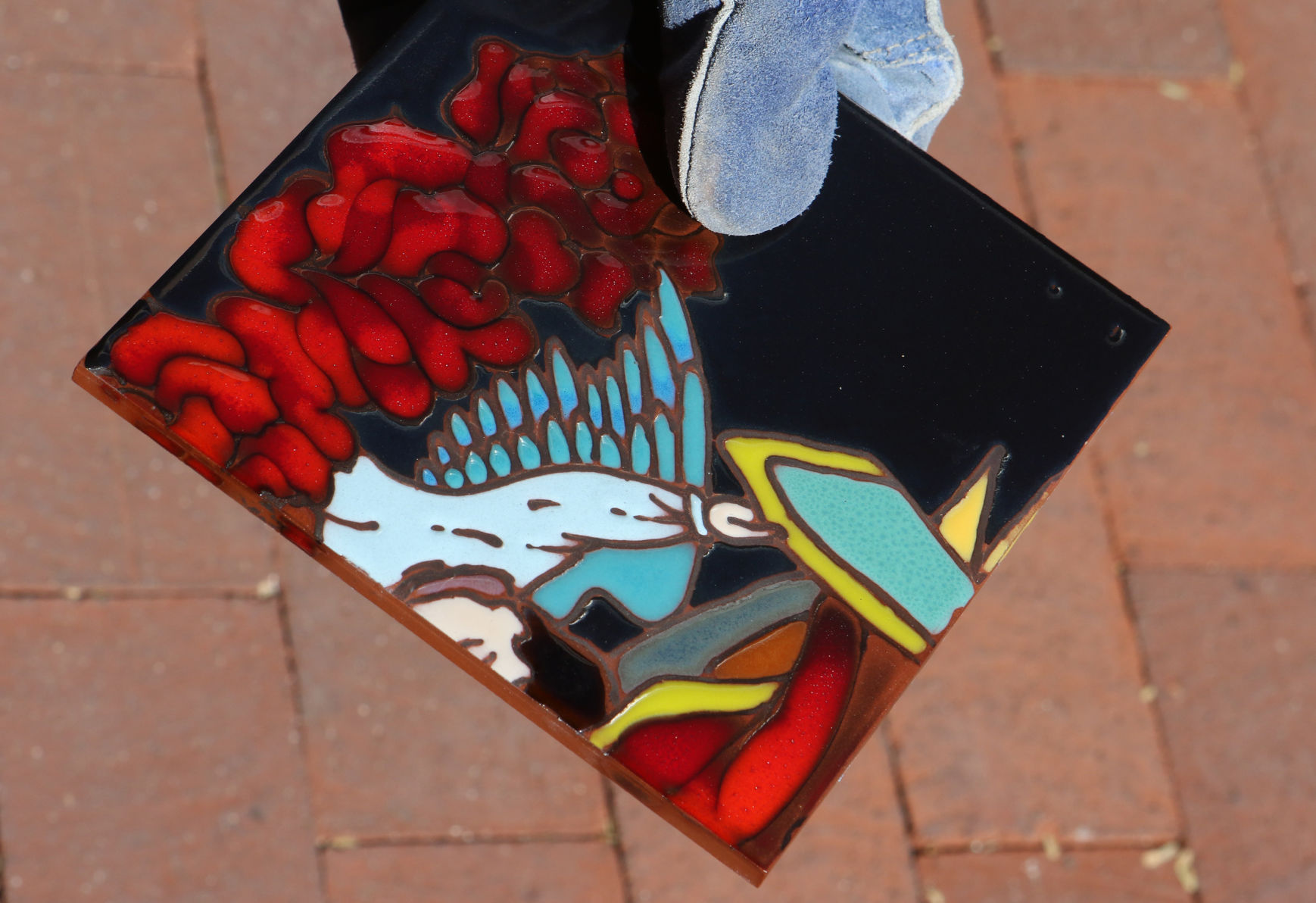
Carly Quinn holds fired tile that is almost ready for assembly.